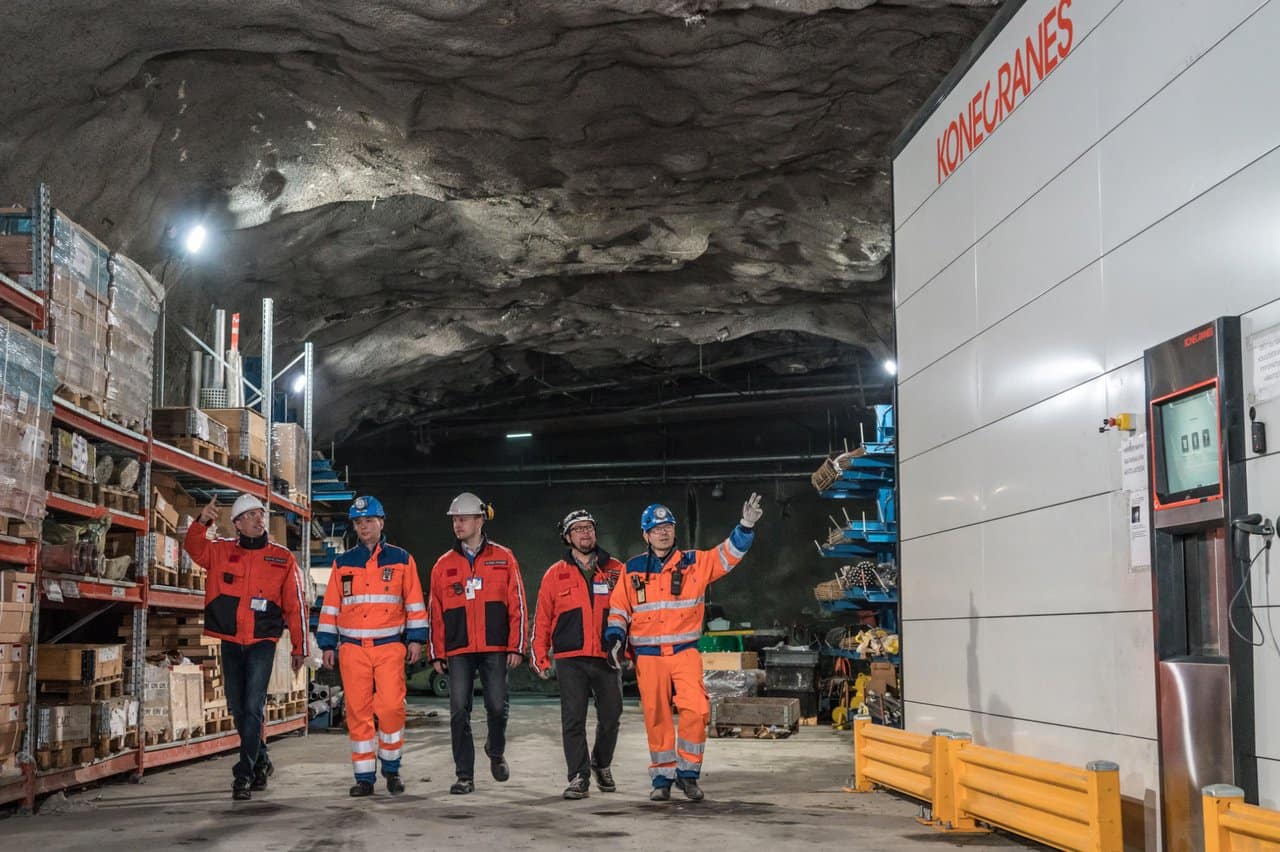
Design makes process industry efficient
Design and machinery in the process industry are not typically associated with each other. At best, industrial environments are perceived as starkly functional. At worst, they are seen as dirty and hazardous. Nevertheless, it is precisely in these environments that design holds a special place—it encompasses much more than just a stylish appearance.
Effectiveness, efficiency, and safety
The development of machinery and equipment in the process industry is driven by economical, technological, and regulatory considerations. Alongside these, the user perspective is crucial. Developing an excellent solution is only possible when the goals, needs, and desires of the users are deeply understood. Feedback from the field, resellers, or internal product development is not enough.
The best starting point for machinery and equipment design is to study workflows in real-use environments. Field visits involve observing and interviewing the people who use the machinery and equipment in their work. In addition to machine operators, it is important to consider other stakeholders in the consumption chain, such as maintenance technicians, installers, supervisors, and decision-makers.
Findings from field visits reveal the aspects that provide the most value. Based on these insights, development work can focus on meaningful areas while giving less attention to less important ones. Often, features that are irrelevant to users can be eliminated. By directing development resources to the right areas from the outset, unexpected (and costly!) changes can be avoided later on.
Analyzing field findings highlights inefficiencies in workflows and guides design towards effective corrections. When the work and its goals are understood, potential conflicts with safety regulations and objectives can be resolved without sacrificing efficiency. Efficient workflows are also pleasant for the users themselves, as unnecessary tasks are eliminated, allowing them to safely focus on the essential. Quick recovery from disruptions reduces downtime and translates to clear financial savings.
Different stakeholders perceive value differently. Purchase decisionmakers appreciate price and efficiency, machine operators value smooth operation and comfort, and maintenance technicians prioritize effective disruption management. A good solution is designed to simultaneously serve all these needs.
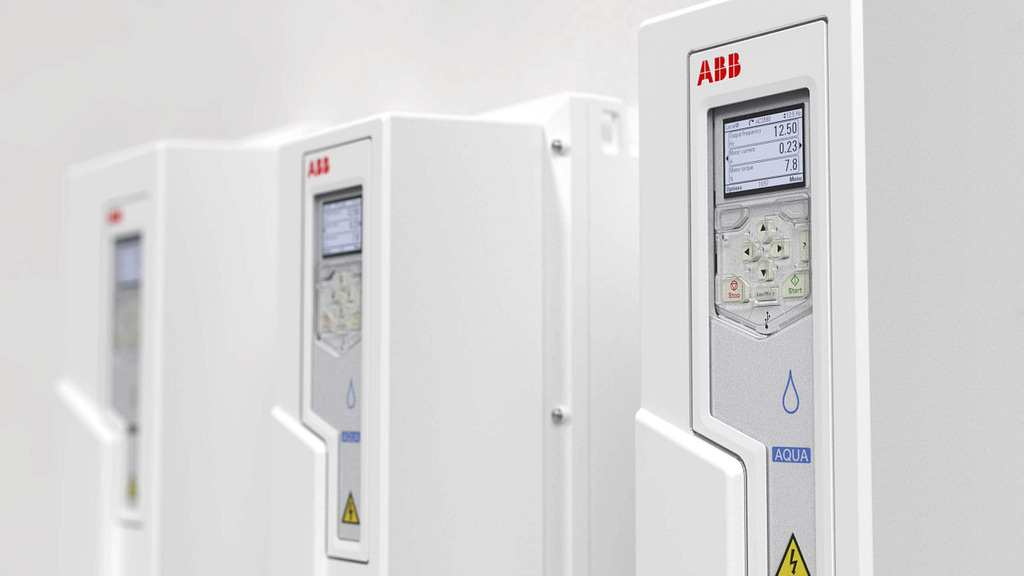
Harmony between machines and control rooms—and everything in-between
In traditional industry, each machine is operated using its control panel, often supplemented with traditional levers and buttons. The same user may operate machines from different manufacturers, each with its own operating logic. In case of disruptions, a maintenance technician is called, who must understand multiple different logics.
The situation becomes more complex when individual machine controls are supplemented with modern control rooms. In the worst-case scenario, machine-specific, differing displays are replicated on the control room wall and workstations as they are. One person must then manage multiple operating logics from different manufacturers, grasp the overall picture, control the process, and respond to anomalies. During disruptions, a technician is deployed to the process, and control from the control room must not endanger their safety. The control room and the machines, as well as any tablet the technician carries, must work together—whether their operating logic is unified or not. The workload on employees is immense.
The solution is to harmonize the user interfaces of digital control systems. This involves designing a comprehensive solution that unifies the operating logic of machine-specific control panels. For control rooms, a solution is designed to provide an informative overview of the entire process and guide the control room operator in making the right decisions. The implementation ensures consistent operating logic everywhere, from display contents to menu structures and user interface components to colors, symbols, and terminology. The tablet carried by the maintenance technician undergoes the same treatment. The impact on work efficiency and safety is substantial.
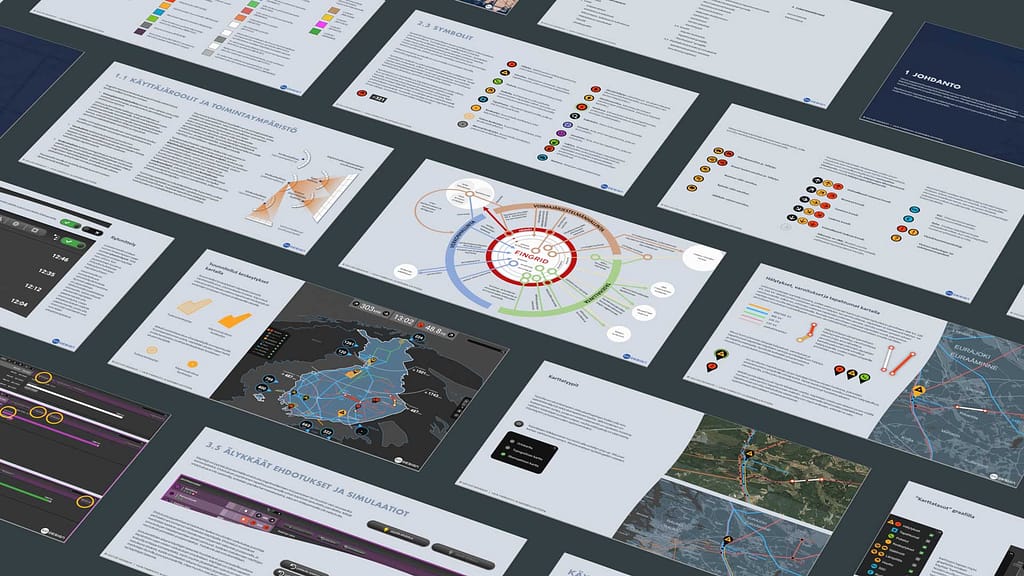
Streamlined looks, streamlined manufacturability
Usability, along with the efficiency and safety it brings, is paramount in factories. The appearance of machinery and equipment should not be underestimated, as it supports the manufacturer’s brand and enhances the credibility of the machines. Whether the customer acknowledges it or not, appearance affects credibility and, consequently, the purchasing decision. A competent design partner ensures that the appearance of the machines is refined in a way that supports usability while reducing manufacturing costs.
Industrial design is design for industry—as long as the design partner is the right one. At Edea, we have carried out several design projects for the process industry or equivalent sectors for companies such as ABB, Cimcorp, Ensto, Evac, Fingrid, Koja, Konecranes, Metso Outotec, Oilon, Oiltanking Finland, Schneider Electric, and Signode Finland.
May we help you too?
-Sami Pyörre / Edea